
Understanding Injection Molding Tonnage
Injection molding tonnage refers to the clamping force required to keep the mold closed during the injection process. Choosing the right tonnage is essential to ensure that the mold remains tightly shut, preventing defects like flash or parting line separation.
A machine’s tonnage rating tells you the maximum clamping force it can apply. Selecting the correct tonnage depends on multiple factors, primarily the projected area of the part and the material being used.
Before getting further into the blog, would you like to know if Injection Molding is the right process for you? Click here to know various Plastic Manufacturing Processes.
Why is Tonnage Important?
If the tonnage is too low, the mold may not stay closed, leading to part defects. On the other hand, using too much tonnage can damage the mold and increase production costs. That’s why it's crucial to calculate the required clamping force accurately.
But before getting in the details, if you would like to know how to make your Injection Molding Project profitable in India, Click here
Understanding Projected Area Calculation
The projected area is the largest surface area of the part viewed from the direction of mold clamping. This is a key value in determining the required clamping force.
How to Calculate Projected Area
The projected area depends on the shape of your part:
Rectangular Part: A = L × W
Circular Part: A = π × r²
For complex parts, you may need to break them into smaller shapes and sum their areas.
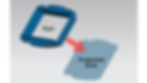
Click here to know the best companies that can calculate Tonnage for you.
How to Calculate Injection Molding Tonnage
Formula 1: General Calculation
The general formula for calculating clamping force is:
Clamping Force (T) = Kp × Projected Area (in²) × Safety Factor (1.1)
Where:
Kp = Material Clamping Force Constant (varies by material)
Projected Area (S) = Surface area of the part viewed from the mold parting line (in²)
Safety Factor = Typically 1.1 to account for variations
Material-Based Kp Values
Each material has a different resistance to flow, which impacts the required clamping force. Below are the approximate values of Kp for different plastics:
Material | Kp (for in²) |
PS, PE, PP | 2.06 |
ABS | 1.93 - 3.1 |
PA, POM, GF-filled plastics | 4.1 - 4.65 |
Other engineering plastics | 4.1 - 5.16 |
Example Calculation
Let's say we have a PE part with a projected area of 63.55 in².
Using the formula:
So, you should select an injection molding machine with 150-170 tons of clamping force to safely mold this part.
Here's a calculator for you :
Formula 2: Using Molding Pressure
Some engineers calculate tonnage using molding pressure instead:
Clamping Force (T) = Molding Pressure (bar) × Projected Area (in²) × 1.1
Example Calculation using 350 bar pressure:
P = 350 × 63.55 × 1.1 / 1000
P = 24.5 T
This method gives similar results and ensures consistency in high-precision applications.
Formula 3: Empirical Calculation
(For Mold Design Phase)
This method helps in early mold design by considering bearing area and inserts.
Empirical Clamping Tonnage Calculation:
Clamping Tonnage = Projected Area × 2 × 1.2
Bearing Area Calculation:
Bearing Area = (Projected Area of Inserts) - (Projected Area of Article)
Projected Area of Inserts is calculated by adding 40 to the length and breadth of the article.
Validation Check:
Clamping Tonnage / Bearing Area ≤ 2 T/in²
If the value exceeds 2 T/in², reduce the Projected Area of Inserts (e.g., reduce the additional 40 to 30 or 20).
Note: This adjustment should be handled during the mold design phase to ensure the correct plate size
Understanding Bearing Area and Inserts
Bearing Area: The contact surface area that resists the clamping force.
Inserts in Injection Molds: Metal parts embedded in the mold to reinforce specific areas or aid in assembly.
Projected Area of Inserts: The surface area occupied by inserts in the mold, impacting force distribution
Choosing the Right Injection Molding Machine
Here are some rules of thumb for selecting the right tonnage:
Low-flow plastics (PA, PC, PSU) → Higher tonnage needed (~4x projected area in in²)
High-flow plastics (PS, PE, PP) → Lower tonnage needed (~2.5x projected area in in²)
Complex parts with deep ribs or high aspect ratio → Add extra safety factor
If your projected area calculation gives you a borderline result, always round up and select a slightly higher tonnage to ensure a stable molding process.
Click here to know the machines available at Plast Fab
Also read our recent blog on insert molding vs overmolding
Conclusion
Understanding and calculating injection molding tonnage is crucial for efficient production and avoiding mold damage. By following these formulas and considering material properties, you can determine the correct tonnage for your injection molding process.
For quick and easy calculations, check out the tonnage calculator Excel sheet attached!
Get Quote for your Injection Molding Project Now!