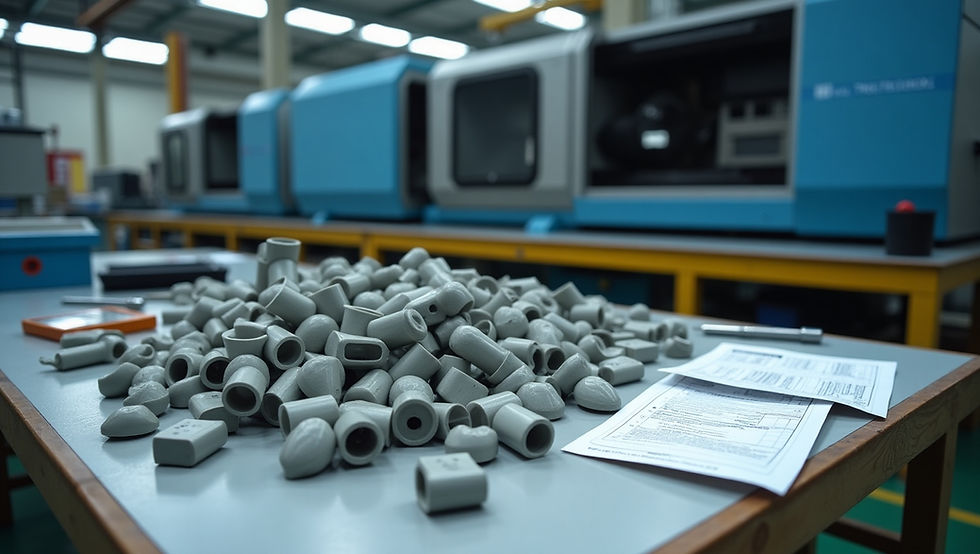
Introduction: A Battle-Tested Guide to Injection Molding Defects
If you’ve spent any time on an injection molding shop floor, you’ve probably dealt with parts that warp like a banana, weld lines so weak they’d snap under a toddler’s grip, or sink marks that make the surface look like a lunar landscape. Injection molding is an art as much as a science—small mistakes in process settings, material selection, or mold design can mean the difference between a flawless part and an expensive rework disaster.
After handling thousands of production runs, I’ve seen it all—parts sticking in the mold like they’ve grown roots, inconsistent dimensions that drive QC teams nuts, and degradation issues that turn a perfect batch into scrap before you can even say "cycle time." The key to mastering injection molding isn’t just knowing how to make good parts, but understanding what causes defects and how to troubleshoot them effectively.
Below is a structured overview of the most common plastic injection molding defects, categorized based on whether they are caused by the mold, the machine settings, or material issues. This guide will help you diagnose and fix problems like a seasoned expert—without pulling your hair out in the process.
Table: Common Injection Molding Defects and Their Causes
Injection Molding Defect | Mold-Related Causes | Machine-Related Causes | Material-Related Causes |
Sink Marks | Non-uniform wall thickness | Injection speed and hold pressure profile issues | Filled polymer can reduce sink marks |
Warping | Poor part stiffness, improper cooling circuit design | Uneven mold surface temperature | – |
Weak Weld Lines | Poor part design | Improper injection speed | – |
Inconsistent Dimensions | Unequal shrinkage due to mold temperature variations | Melt temperature, injection speed, and hold pressure | Check material shrinkage characteristics |
Material Degradation | Incorrect runner system dimensions leading to excess shearing | Oversized injection unit causing excessive residence time | Check polymer thermal stability and additives |
Ejection Difficulty | Unbalanced melt flow | – | – |
Poor Impact Strength | Sharp corners acting as stress concentrators | – | Consider high molecular weight polymers |
Inconsistent Weight | – | Shot capacity near 90% utilization causing melt inconsistency | – |
Inconsistent Filling | Small gate size causing high pressure drop | Insufficient injection rate for required flow ratio | – |
Stress Cracking | Unbalanced melt flow | Overpacking due to incorrect pressure settings | – |
Dimensional Variation | – | – | Check material shrinkage characteristics |
Difficulty in Filling | – | – | Use a higher Melt Flow Index (MFI) polymer |
Sink Marks : The Hidden Battle of Plastic Injection Molding

Introduction
Sink marks are the silent killers of perfect aesthetics in plastic injection molding. They appear as depressions or indentations on the surface of molded parts, particularly in areas where wall thickness varies significantly—such as ribs and bosses.
While process tweaks like reducing melt temperature or increasing hold pressure might help, the root cause often lies in part design.
Why Do Sink Marks Occur?
When thick sections of a part cool and shrink unevenly, the outer layer solidifies first while the inner material continues to contract, pulling the surface inward.
The volumetric shrinkage of plastic from melt to solid is 25-30%, while the compressibility of melt at injection molding pressure is only 15%, making it impossible to fully eliminate sink marks by simply increasing pressure.
If the rib thickness exceeds 0.6 times the main wall thickness, excess material at the junction shrinks, causing voids that lead to visible sink marks.
How to Avoid Sink Marks?
Maintain Proper Rib Thickness: Keep the rib thickness between 0.5 to 0.6 times the main wall thickness to minimize shrinkage effects.
Reduce Melt Temperature: Lower melt temperatures can reduce overall shrinkage.
Optimize Hold Pressure & Time: Applying sufficient hold pressure can help compensate for material shrinkage, but it won’t eliminate sink marks entirely if the design is flawed.
Design with Gradual Transitions: Sudden changes in wall thickness create stress points that worsen sink marks—opt for smooth transitions.
Use Higher Packing Efficiency Materials: Some materials exhibit lower volumetric shrinkage, reducing the tendency for sink marks.
Conclusion on Sink Marks
Sink marks are primarily a design issue, not just a processing problem. While minor adjustments in temperature and pressure can help, the most effective solution is ensuring correct rib and wall thickness proportions during the design phase. If your mold is already built, addressing sink marks may require compromises between aesthetics and structural integrity—a lesson learned after years on the shop floor!
Warpage: The Unwanted Twisting in Injection Molding
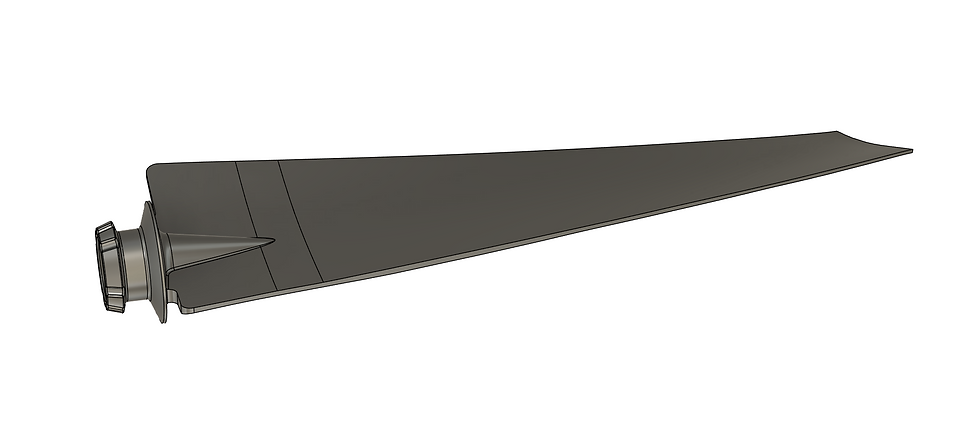
Introduction
If you’ve ever molded a supposedly “flat” part only to see it come out looking like a potato chip, congratulations—you’ve met warpage. It’s the silent nemesis of injection molders, causing parts to bend, twist, or curl in ways that make assembly a nightmare. Unlike some other defects, warpage is a complex beast, influenced by shrinkage variations, cooling inconsistencies, and material orientation effects. Fixing it? That’s where experience (and a good CAE analysis) comes in handy.
Why Does Warpage Occur?
Differential Shrinkage: When different areas of the part shrink at different rates, internal stresses cause deformation.
Orientation Effect: Polymer chains shrink more in the flow direction than perpendicular to it, creating internal stress imbalances.
Differential Cooling: Uneven cooling inside the mold results in hot and cold zones, leading to inconsistent shrinkage across the part.
Area Shrinkage Effect: Variations in shrinkage between the central and peripheral areas of a part can result in dome-like or saddle-shaped warping.
Geometric Stiffness: If a part has high shrinkage variation but is structurally rigid, it may not warp, but will instead trap high residual stress—which can cause cracks or failure later.
How to Avoid Warpage?
Improve Mold Cooling Design: Uniform mold temperature distribution reduces differential cooling effects.
Optimize Wall Thickness: Increase thickness near the gate to counteract shrinkage due to orientation and at the flow ends to balance area shrinkage.
Add Structural Support: Ribs and curved surfaces increase stiffness, reducing warpage susceptibility.
Use CAE Warpage Analysis: Advanced simulations can predict warpage and optimize mold design before production begins.
Balance Packing Pressure: Overpacking one area while underpacking another can cause uneven shrinkage—ensure uniform pressure distribution.
Conclusion on Warpage
Warpage isn’t just a minor annoyance—it’s a dealbreaker for precision components. While some may try to tweak processing parameters, the real solution lies in design and mold cooling. Whether it’s optimizing rib placement or running a warpage analysis in CAE software, tackling this defect early in the design phase will save time, money, and frustration down the line. And trust me, after a few warped batches, you’ll learn to appreciate the beauty of good mold temperature control! Read this blog on how auxiliary equipment can help.
Weld Lines: The Weak Links in Plastic Injection Molding

Introduction
Ever noticed those faint, hairline seams on molded parts that just don’t look right? Those are weld lines—the result of multiple melt streams coming together and failing to merge seamlessly. Think of them as the "cold handshake" of the injection molding process, where two streams meet but never truly bond. While they might seem harmless, weld lines weaken the structural integrity of the part, reducing its impact resistance and making it prone to failure under stress.
Why Do Weld Lines Occur?
Opposing Melt Streams: When two plastic streams meet head-on, their interface remains a weak point since molecular chains align perpendicular to the flow direction.
Wall Thickness Variations: Inconsistent wall thickness can lead to uneven flow speeds, creating weld lines in unexpected areas.
Multiple Gates: While useful for reducing flow length, multiple gate designs often create more weld lines, which may weaken the part.
Low Melt Temperature or Injection Speed: If the plastic is not hot enough or injected too slowly, it lacks the energy to fuse properly at the weld line.
How to Avoid or Strengthen Weld Lines?
Optimize Gate Placement: Position gates so that weld lines form in non-critical areas where strength is not a primary concern.
Increase Melt Temperature: Hotter material has better flow properties, leading to stronger fusion at weld lines.
Boost Injection Speed: Higher speeds ensure that melt streams join before they begin to solidify, improving molecular bonding.
Modify Wall Thickness: Balancing wall thickness helps regulate flow speed, preventing premature solidification at the weld interface.
Adjust Switchover Position: Shifting the transition from injection to hold pressure toward zero ensures better packing in weld line regions.
Increase Mold Temperature: A well-heated mold promotes better adhesion between melt fronts, strengthening weld lines.
Conclusion on Weld Lines
Weld lines are inevitable in injection molding, but poorly placed or weak weld lines can be disastrous for product strength. While complete elimination is unrealistic, strategic mold and part design choices can significantly reduce their impact. As a molder, I’ve learned that tweaking parameters like injection speed, melt temperature, and gate locations can make a world of difference. Because trust me, the last thing you want is a part that breaks right along the weld line—that’s a defect waiting to happen!
Stress Cracking: The Silent Killer of Plastic Injection Molded Parts
Introduction
If you’ve ever had a customer call you up complaining that their plastic containers mysteriously cracked in service, welcome to the club! Stress cracking is one of the most frustrating defects in injection molding—because the part looks fine when it leaves the machine, but weeks or months later, it fails. It’s like sending your kid off to college, thinking they’re doing great, only to find out they’ve been living on instant noodles and making poor life choices.
Stress cracking is caused by molded-in residual stress, which weakens the polymer structure over time. This stress builds up due to overpacking, unbalanced flow, or uneven cooling—and if external factors like chemicals or mechanical loads come into play, cracks begin to form. The worst part? By the time the cracks appear, the damage is already done. This happens majorly in insert-molded and overmolded parts.
Why Does Stress Cracking Occur?
Overpacking During Molding: Excessive pressure during injection creates residual stress in the plastic, making it prone to cracking.
Unbalanced Melt Flow: If certain regions fill before others, the earlier-filled areas get compressed while waiting for the rest of the melt to arrive.
Uneven Cooling Rates: Parts of the mold that cool at different speeds create internal stress, which can lead to cracks over time.
Chemical Exposure: Some plastics, like PC, ABS, and HIPS, are highly prone to environmental stress cracking when exposed to detergents, solvents, or oils.
How to Avoid Stress Cracking in Injection Molded Parts?
Optimize Packing Pressure: Use just enough follow-up pressure to avoid sink marks, but not so much that it overpacks the part.
Ensure Balanced Flow: Use flow leaders or flow deflectors in mold design to ensure that all sections of the part fill evenly.
Control Cooling Uniformly: Design molds with consistent temperature distribution to avoid stress buildup.
Choose the Right Material: If a part will be exposed to chemicals, test its resistance beforehand—materials like PC and ABS blends are particularly vulnerable.
Perform CAE Simulations: Melt flow analysis can help predict and mitigate potential stress concentrations before production even begins.
Conclusion on Stress Cracking
Stress cracking is one of the leading causes of plastic part failures, and unfortunately, there’s no quick fix after molding. At Plast Fab, we learned this the hard way when a batch of detergent container lids came back with mysterious fractures. Turns out, our polycarbonate lids were reacting with the detergent chemicals, leading to stress-induced fractures. After this costly mistake, we switched materials and added melt flow simulations to our design process, eliminating the issue altogether. Lesson learned: a little foresight in material selection and mold design can save you from a world of trouble later on.
Shrinkage in Plastic Injection Molding: A Necessary Evil

Introduction
Shrinkage is one of those things in injection molding that you just have to live with—like taxes or long customer negotiations. No matter how precisely you mold a part, the moment it cools, it shrinks—and sometimes not in the way you want it to. Shrinkage is unavoidable, but controlling it is what separates a good molder from a great one.
Over the years at Plast Fab, we’ve battled shrinkage in countless ways, from tweaking hold-on pressures to adjusting cooling rates. And while some shrinkage is inevitable, ignoring it can lead to warped, dimensionally inconsistent parts that simply won’t fit where they’re supposed to.
What Causes Shrinkage?
Shrinkage is influenced by a range of molding parameters, material properties, and part design factors:
Thermal Expansion & Cooling → Plastics shrink as they cool, and crystalline plastics shrink more due to phase transition.
Hold-on Pressure & Time → Controls how much material compensates for shrinkage before solidification.
Melt Temperature → Higher temperatures increase shrinkage as the polymer cools.
Mold Temperature → Warmer molds lead to slower cooling, allowing for more shrinkage.
Wall Thickness & Distance from Gate → Thicker sections and areas further from the gate experience more shrinkage.
Shear Rate & Fill Speed → Shear-thinned melt flows differently, affecting how uniformly it cools and shrinks.
How to Minimize Shrinkage in Injection Molding?
Optimize Packing Phase: Maintain hold-on pressure until the gate freezes to prevent material from flowing backward into the nozzle.
Balance Mold Cooling: Ensure consistent mold temperature across the part to promote uniform shrinkage.
Control Gate Size: A larger gate allows better pressure transmission, reducing localized shrinkage.
Modify Processing Conditions:
Increase hold-on pressure and time.
Reduce melt temperature.
Adjust injection rate for even material flow.
Choose the Right Material: Amorphous and reinforced plastics shrink less than crystalline polymers.
Conclusion on Shrinkage
Shrinkage might be inevitable, but dimensional disasters don’t have to be. At Plast Fab, we once molded a large structural component for an industrial client that had to fit with extreme precision. Initially, the shrinkage varied so much that the parts were out of spec. The solution? Tweaking the packing pressure, adjusting gate sizes, and optimizing the cooling cycle—and suddenly, we had parts that fit like a glove.
Shrinkage is not the enemy—uncontrolled shrinkage is. The key is understanding it, predicting it, and managing it before it manages you.
good info, will surely keep these points in mind before designing parts for plastic injection molding